Power Module
The Power Module available for MakaiPlan, MakaiPlan Pro, and MakaiLay includes a collection of tools that were developed for addressing specific issues faced by submarine power cables during installation. Power cables are heavier and more rigid than fiber optic cables. Their longevity can be severely compromised if they are not installed with the correct tension on the seabed. Thus, a successful power cable installation requires more careful planning and monitoring.
Available for…
Now Available for MakaiPlan, with Heave and Span Analysis!
Other Modules Available
MakaiLay Power: Subsea Power Cable Control Software
Fiber Optic Cables Versus Power Cables
Power cables are considerably heavier and more stiff than fiber optic cables. While fiber optic cables are installed with slack on the seabed, power cables have to be installed with some residual tension to avoid a bend radius smaller than the Minimum Bend Radius (MBR) recommended by the manufacturer, which could kink and damage the cable at the touchdown (as seen in Figure 1 below).
Due to the fact that conventional installers of power cables do not have the means to accurately estimate the cable tension on the seabed, they operate with very high safety factors. Consequently, power cables are usually installed with tensions that are much higher than the required values. Cable suspensions occur more often than desired as a result. As shown in Figure 2, at these seafloor contact points, large reaction forces and small bend radii are common, thereby reducing the life expectancy of the cable due to increased wearing and chafing.
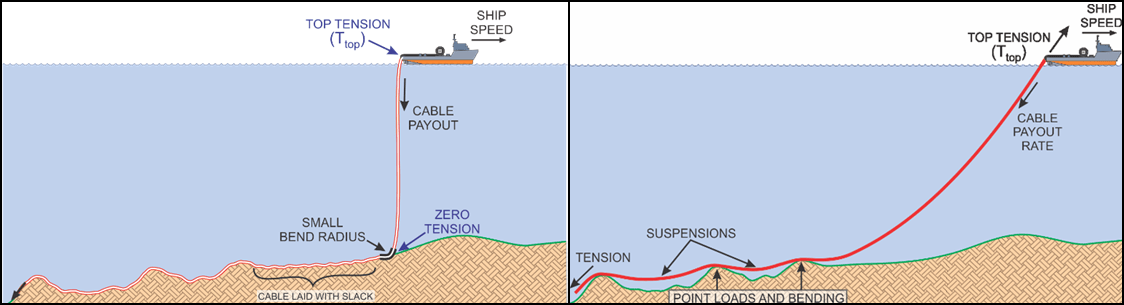
Figure 1 (left): Too little bottom tension or bottom slack will cause excessive bending of the cable.
Figure 2 (right): Too much bottom tension will create spans on the bottom creating heavily loaded contact points.
To maximize the life expectancy of the cable, the power cable installer must accurately lay the cable with low values of bottom tension to avoid cable suspensions, but at the same time maintain a small amount of tension at the touchdown to maintain bend radii above the MBR. The bottom tension and cable touchdown location can be accurately managed using MakaiPlan Pro and MakaiLay with the Power Module, both of which have the capability to accurately model the 3D cable shape, touchdown location, and tension on the seabed during a lay.
Features
ROV Tracking
Most power cable lays have an ROV tracking the cable touchdown point during the installation. Makai can now log and use the USBL coordinates of the ROV in real-time to improve the cable shape calculation. The ROV tracking feature enables installers to use the real-time position feedback from the ROV to improve the cable shape calculation.
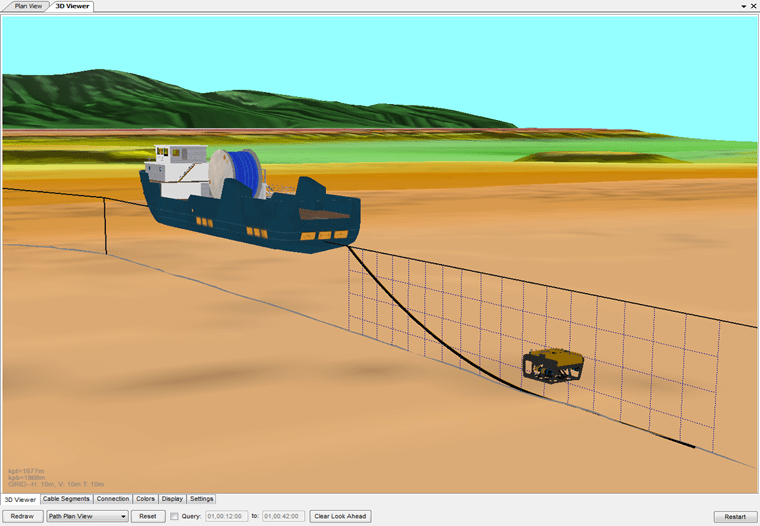
3D Geospatial Viewer
The 3D viewer was updated to include more realistic views of the vessel, cables, seafloor, ocean surface and other GIS information that will build the installation scene clearly for the cable installer. The new viewer will be a true GIS-based viewer where all the features displayed are properly geo-referenced in a Lat/Lon or a grid coordinate system. Makai’s 3D Geospatial Viewer shows clear installation scenes with realistic vessel, plough, terrain and cable shapes.
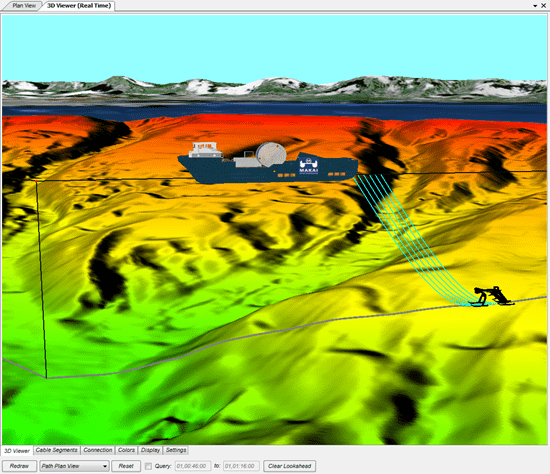
Auto-Tension Tool
Auto-Tension is an extension of the Look-Ahead module which allows the users to vet and optimize future ship instructions. Using the Auto-Tension tool, users can automatically generate future cable pay-out instructions that will maintain a desired bottom tension during the installation.
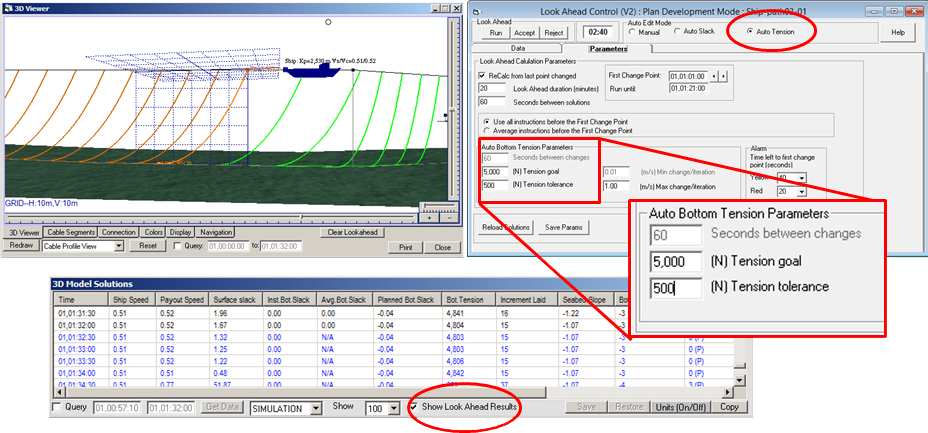
Top-Angle Measurement Input
In shallow waters, the top cable angle or the departure angle measured at the cable overboarding point is sensitive to the changes in tension at the cable touchdown point. Top angle measurements can now be used as an input to the Makai’s real-time cable model to calculate the cable shape, touchdown position and bottom tension.
Span Analysis Tool
Using this tool, cable engineers can calculate the true shape of the cable on the seafloor when different tensions are maintained on the cable. The model accurately calculates the resulting free spans, the reaction forces on the cable at the seafloor, bend radii, and shear forces and moments along the suspended cable. The tool can provide the cable engineer with values of the bottom tension that need to be maintained during installation in order to avoid excessive spans on the seafloor. The Span Analysis tool comes with Power modules for MakaiPlan, MakaiPlan Pro, and MakaiLay.
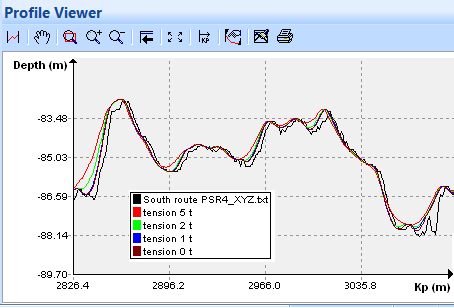
Heave Analysis Tool
As a ship heaves up and down with the waves, cable tension and bend radius of the cable catenary can be impacted, potentially damaging the cable. To simulate these effects on the cable, a Heave Analysis tool comes with the Power modules for Makai Plan, MakaiPlan Pro, and MakaiLay. This tool enables users to perform analyses for different sea states and lay conditions to ensure that tensions and bend radii are within allowable limits during the installation. Users can import the vessel RAOs and impose wave spectra to create realistic ship motions (heaving, pitching, etc.) and then analyze the impact on cable tensions and bend radii. The tool can be used in office to design a safe lay with MakaiPlan Pro, or at-sea with MakaiLay to make fast decisions about the lay as conditions change and contingencies arise.
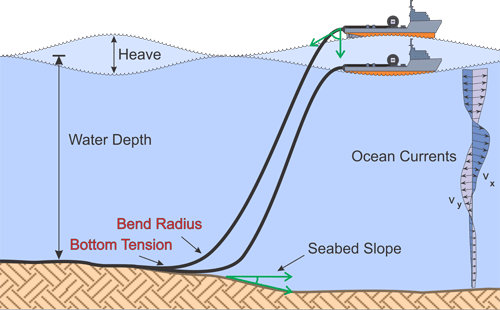
Issues with Traditional Installation Methods
Traditional installation methods often result in large cable suspensions which reduce the lifespan of the cable. The key to minimizing suspensions is to accurately control the cable tensions at touchdown. However, due to the lack of measurement capabilities, tension at touchdown is calculated from measured top conditions of the cable.
The tension of the cable at the seabed can, very closely, be estimated by the simple relationship: Ttop = Tbot + WxH
where Ttop is the top cable tension (measured at the vessel), Tbot is the cable tension at the touchdown, W is the cable wet weight per unit length and H is the water depth at the touchdown (see figure to the right). This simple relationship is useful for calculating cable bottom tension only when installing the cable in relatively shallow waters and on a flat seabed. In mid- and deep waters, the weight of the suspended cable in the water column (WxH) tends to be considerably larger than the desired value of bottom tension, and in most cases the noise in the measurements of top tension (due to cable and ship dynamics) is equal to or larger than the low values of Tbot the installer wants to maintain. Therefore, simply measuring Ttop does not provide a good method to estimate the values of bottom tension.
In addition, not having an accurate model of the cable dynamics in the water column can introduce large errors in the exact location of the cable touchdown, so while laying up-slopes or down-slopes, these errors can quickly affect the true touchdown depth, H, and consequently the estimated values of Tbot. A typical example is when laying cable down the slope. If the operator wants to decrease the value of bottom tension, the logical step is to pay out more cable at the surface. However, in this case the cable touchdown becomes deeper and the Ttop increases. As the tension increases, the operator thinks he should pay out more cable to decrease the tension, but this only makes the situation worse.
Another common practice of estimating bottom tension is by using the cable angle at the sheave. In shallow waters, the cable angle is more sensitive to the changes in cable bottom tension so this method works. However, in deep waters, the cable enters the water almost vertically and is very insensitive to changes in cable bottom tension, therefore, the value of cable angle does not provide accurate feedback on cable tension.
A cable control system can accurately model the cable touchdown and bottom tension, both of which are essential to properly install power cables.
Interested in Makai’s Submarine Cable Software and Services?
ReACH OUT!
Contact us by sending in this form any time you need professional support or have any questions. You can also fill in the form to leave your comments or feedback for Makai’s team.